What is Porosity in Welding: Crucial Tips for Getting Flawless Welds
What is Porosity in Welding: Crucial Tips for Getting Flawless Welds
Blog Article
The Science Behind Porosity: A Comprehensive Guide for Welders and Fabricators
Comprehending the detailed mechanisms behind porosity in welding is critical for welders and fabricators making every effort for flawless craftsmanship. From the composition of the base materials to the intricacies of the welding procedure itself, a plethora of variables conspire to either worsen or minimize the visibility of porosity.
Understanding Porosity in Welding
FIRST SENTENCE:
Evaluation of porosity in welding discloses critical understandings right into the stability and top quality of the weld joint. Porosity, characterized by the visibility of tooth cavities or voids within the weld metal, is a common concern in welding procedures. These gaps, otherwise correctly resolved, can compromise the architectural honesty and mechanical buildings of the weld, leading to potential failings in the completed product.

To find and measure porosity, non-destructive screening approaches such as ultrasonic screening or X-ray evaluation are frequently utilized. These methods permit the identification of inner problems without jeopardizing the stability of the weld. By evaluating the dimension, form, and circulation of porosity within a weld, welders can make enlightened choices to enhance their welding procedures and accomplish sounder weld joints.
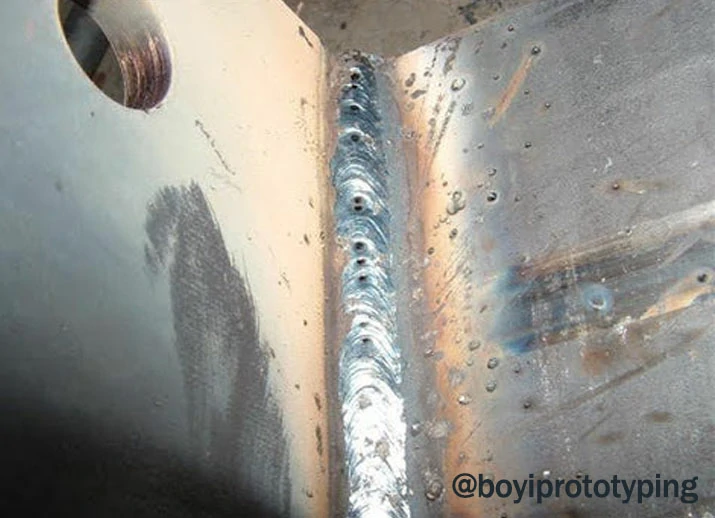
Aspects Influencing Porosity Development
The incident of porosity in welding is affected by a myriad of factors, varying from gas shielding efficiency to the complexities of welding specification settings. Welding criteria, consisting of voltage, current, travel speed, and electrode type, likewise influence porosity development. The welding strategy utilized, such as gas metal arc welding (GMAW) or protected steel arc welding (SMAW), can influence porosity development due to variations in warm circulation and gas coverage - What is Porosity.
Effects of Porosity on Weld Top Quality
The existence of porosity additionally compromises the weld's resistance to rust, as the trapped air or gases within the voids can respond with the surrounding environment, leading to deterioration over time. Furthermore, porosity can hinder the weld's capacity to stand up to stress or effect, further endangering the overall high quality and integrity of the welded framework. In crucial applications such as aerospace, automobile, or architectural building and constructions, where security and longevity are critical, the detrimental results of porosity on weld top quality can have serious effects, stressing the relevance of lessening porosity with appropriate welding strategies and procedures.
Strategies to Reduce Porosity
To enhance the top quality official statement of welded joints and make certain structural honesty, welders and makers employ certain methods targeted at reducing the development of spaces and dental caries within the material during the welding procedure. One effective technique to decrease porosity is to make sure proper material prep work. This consists of complete cleansing of the base steel to get rid of any type of contaminants such as oil, oil, or dampness that might add to porosity development. Additionally, making use of the suitable welding specifications, such as the correct voltage, existing, and travel rate, is critical in avoiding porosity. Maintaining a regular arc size and angle throughout welding likewise helps in reducing see the chance of porosity.

Moreover, selecting the appropriate securing gas and maintaining proper gas flow rates are essential in decreasing porosity. Using the ideal welding method, such as back-stepping or utilizing a weaving movement, can additionally help distribute heat evenly and minimize the chances of porosity formation. Finally, making sure proper air flow in the welding setting to eliminate any kind of potential resources of contamination is crucial for accomplishing porosity-free welds. By executing these strategies, welders can successfully lessen porosity and create premium welded joints.

Advanced Solutions for Porosity Control
Executing innovative modern technologies and ingenious approaches plays an essential role in attaining exceptional control over porosity in welding procedures. Additionally, utilizing sophisticated welding methods such as pulsed MIG welding or customized ambience welding can also aid mitigate porosity concerns.
An additional advanced service involves making use of sophisticated welding devices. For circumstances, making use of devices with built-in attributes like waveform control and innovative source of power can improve weld high quality and minimize porosity risks. In addition, the implementation of automated welding systems with specific control over criteria can dramatically decrease porosity defects.
Furthermore, including advanced surveillance and assessment modern technologies such as real-time X-ray imaging or automated ultrasonic screening can aid in detecting porosity early in the welding procedure, permitting prompt restorative actions. On the whole, incorporating these advanced remedies a knockout post can significantly improve porosity control and enhance the total quality of welded parts.
Conclusion
To conclude, recognizing the science behind porosity in welding is necessary for welders and makers to produce top quality welds. By recognizing the factors affecting porosity development and carrying out techniques to lessen it, welders can improve the total weld high quality. Advanced services for porosity control can better enhance the welding procedure and ensure a strong and trusted weld. It is very important for welders to constantly inform themselves on porosity and implement best methods to accomplish optimal outcomes.
Report this page